SID-TEC does a complete motor controls
update of Duke Energy’s main line
SA Trenching Stacker Reclaimer machine…
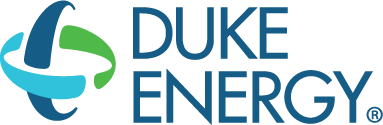
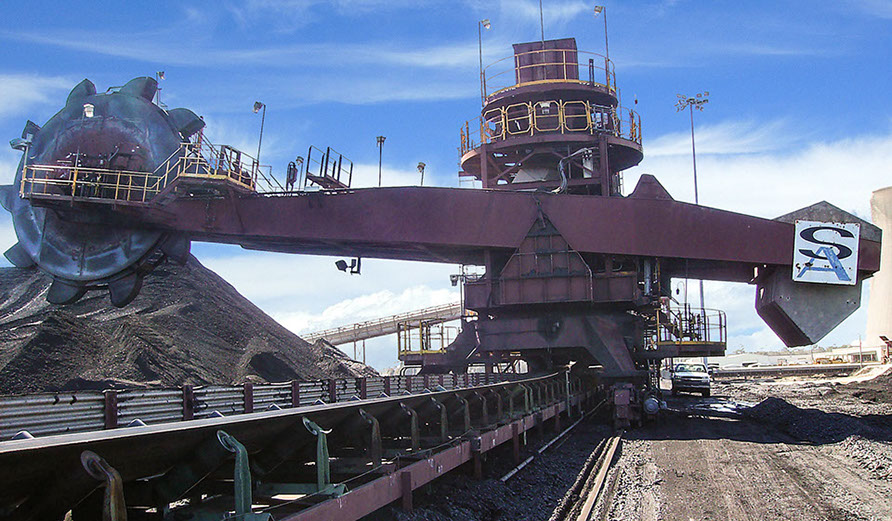
ABOVE: Duke Energy’s huge coal trencher/reclaimer dwarfs the full-sized pickup truck parked next to it. The machine required a complete retrofit of a series of new electric motors and control panels which provided smooth operation and eliminated downtime.

The 6 DC travel motors were brought into coordinated control instead of working against each other at different speeds and power levels, allowing reduced wear and tear on equipment
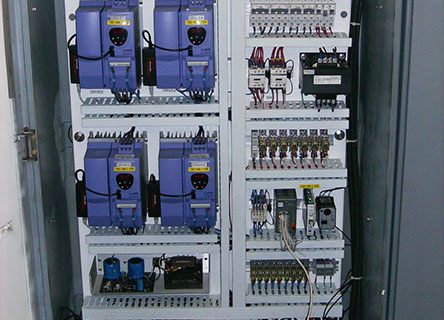
A fully upgraded and updated control panel now replaces equipment no longer available from the original manufacturer. Ease of use removes potential operator fatigue.
PROJECT CHALLENGES
Duke’s gargantuan Crystal River stacker/trencher machine had serious productivity issues due to outdated motors and controllers requiring regular downtime and maintenance. SID-TEC was able to quickly diagnose the problems, install updated equipment and train the staff in its operation.
1 — Travel Drives and Motors Problems
The SA stacker/trencher machine had been built with 6 DC Shunt Wound Motors fitted with oversized brakes. The motors were all being controlled by a single Saftronics DC Drive with a separate field current controller to control all of the motors shunt fields. All of the motor armatures were connected to the single DC Drive armature circuit using individual by-metal overload units and fuse protection in the event of a motor or cable fault. Each of the individual motor Shunt Field circuits were connected to an adjustable field current balancing resistor. This is not an uncommon type of control system for older machine designs, but it does have some distinct drawbacks and related problems.
In a Shunt Wound DC Motor the field current (also known as the excitation) sets the top speed of the motor speed range, while the armature voltage is proportional to the speed of the motor. The top speed for the motor is set by the amount of current being put into the Shunt Field.
The 6 travel motor wheels all have one thing in common, they are all physically connected to the rails of the railroad tracks, and due to very heavy weight of the machine, they have a very strong connection and it is not possible for them to slip. This means that all the motors have to be set to run at the exact same speed. This means that motors which run slower than the others will not take the load or do any work of propelling the machine, Any motor which is set faster will try to do all the work, taking all the load required to propel the machine up and down the tracks, this will overload the motor and cause it to be damaged due to excessive load and heat.
The result is that if a motor or motors are changed out or replaced, then all the motor shafts have to be disconnected from the gearboxes and the machine run so that each motor can get its shunt field balancing resistor adjusted and set so that all the motors run at exactly the same speed. This takes a lot of time and is a difficult job to perform — which is why it is seldom done — because power has to be removed every time a resistor is adjusted and then power re-applied to verify the result of the adjustment. DC motors also require service to check the brushes and clean the loose carbon dust out of the motor. Failure to do this will cause damage to the commutator if the brushes wear out or cause overheating if the cooling veins become choked with dirt and brush carbon.
This is a main line machine within the power plant’s operation. It is used to stack coal when there is an abundance and to supply coal to the power station when there is a shortage or delay in the delivery of new coal to the facility. The reliability of this machine is a high priority for the power generation plant.
SID-TEC’s solution and specifications clear away the problems
SID-TEC provided Duke Energy with a solution and a quotation to resolve all of the above problems. SID-TEC was awarded to contract to replace all of the travel drives and motors.
SID-TEC provided the motor manufacturer with the specification to design and build a set of Vector Inverter duty motors with oversized shafts and brakes that would match the full output torque of the motor at 1200 RPM while full speed of the motor was 1800RPM.
Every AC Induction motor has a percentage of magnetic slip between the stator (the stationary frame of the motor) and the rotor (the rotating part connected to the output shaft). The slip of the output of these motors were designed so that they would share the load without the necessity of any additional individual control adjustments.
The single DC Drive and back plate with all the controls was removed and a new back plate housing 6 Open Loop Vector AC Drives was installed. This meant that each individual motor was now being controlled and protected by its own AC drive. Each of the 6 drives were set up with Ethernet control cards and added into a LAN (Local Area Network) along with a UPC (Universal Process Controller). This was done to ensure that each of the drives and motors would run at exactly the same speed.
The advantages of this new system are that all of the motors share the load automatically during the traveling of the machine and if some coal gets onto the rail and jambs the motor wheel, the individual drive trips out, protecting the motor while the machine continues to work as normal on the 5 remaining drives and motors. If a drive trips out, an alarm is sent and at a convenient time the service personnel can reset the drive and the machine put back into service with all drives and motor running.
The system has operated flawlessly and the customer is very satisfied. The machine reliability has been restored and the need for constant maintenance has been removed.
2 — Slew Drive

The Slew Drive function was using a Saftronics M12 DC Drive and a separate shunt field regulator. These products are no longer supported by the manufacturer so this was a major concern for Duke Energy. We were ordered to replace this equipment with a product that will be supported and continue to be supported into the future.
The new DC drive is fully digital and it has the shunt field regulator built into the drive as a complete package, so no loose or separate parts are required.
SID-TEC built a complete new unit on a replacement back plate to allow for an easy exchange. The drive was fitted with an Ethernet communications card, the control signals were put into a UPC and both were connected into the LAN network.
3 — Bucket Wheel Drive

The Bucket wheel function was using a Saftronics M6 DC Drive and a separate shunt field regulator. These products are also no longer supported by the manufacturer so they were also replaced by SID-TEC with a with current DC Drive product that is and will be supported for the next 25 years or more.
The motor is a compound-wound DC motor and had been fitted with an analog tachometer in use as a speed feedback signal. In addition the motor was totally enclosed and fitted with a heat exchanger for cooling.
We put a heavy duty encoder onto the back of the motor in place of the analog tachometer the benefits are that there are no brushes in the encoder and the signal is digital and so is not affected by induced electrical noise which used to effect the speed accuracy of the bucket wheel during the dig cycle where the load is erratic because of the buckets as they enter the coal pile.
The new DC Drive is fully digital and has the field regulator built into the drive as an integral part, so there are no separate parts to the motor controller and everything is being regulated by the drive. In addition the drive has been fitted with an Ethernet card and uses a UPC as an interface to the main control systems PLC. There is an added benefit in the form of the LAN network which now includes all the drives and control functions which can be viewed by connecting to the network.
CLIENT TESTIMONIAL:
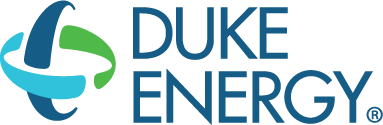