Upgrading controls for the main bascule bridge at NASA’s Stennis Space Center rocket testing site
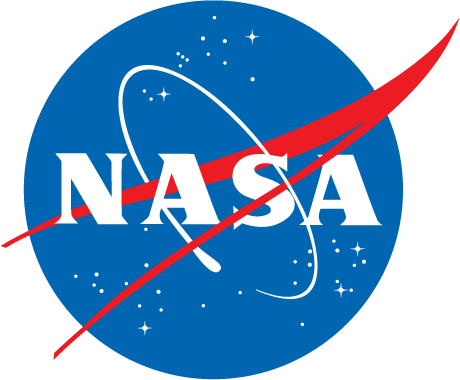
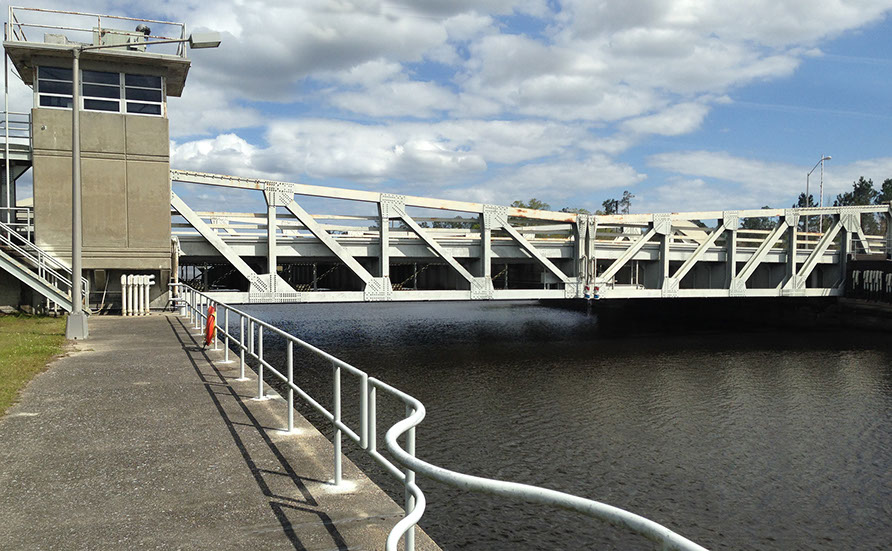
ABOVE: NASA’s Stennis Space Center’s large bascule bridge which crosses the locks and the Pearl River canal. SID-TEC was awarded the contract to design, build and program all of the control equipment used for the raising and lowering of the bridge. The bridge is used to haul rocket engines and all road-shipped equipment into the facility. The river, locks and canals are used to ship rocket fuel and other equipment onto the site by barge. The bridge raises to allow barges and equipment to pass safely under it.
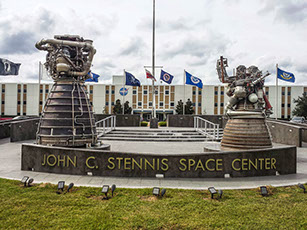
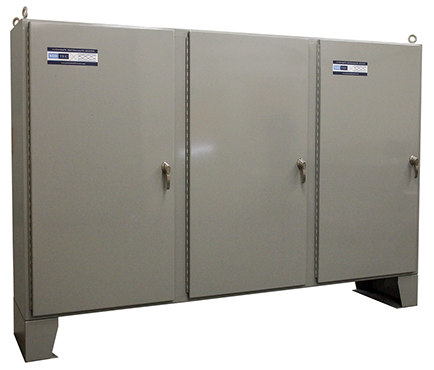
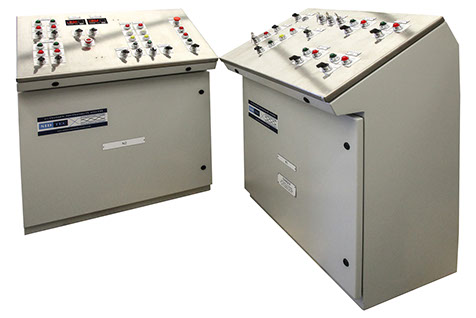
ABOVE LEFT & BELOW CENTER: These are photos of the two identical north and south span motor control enclosures. These custom high-tech enclosures were designed & engineered by SID-TEC’s engineering department and the designs were sent out for manufacture. The enclosures are constructed of heavy gauge stainless steel to comply with NASA specifications, and have been treated with special heat transferring powder coat. The three sections are manufactured into one enclosure, where the entire surface area of the enclosure acts as a cooling system. The internal air of the enclosure is circulated between the three sections by means of fans mounted in the center side walls, the cooling fans are turned on during the operation of the equipment to circulate and dissipate the heat created.
This cooling method was chosen in preference to the use of air conditioners which cause condensation to form by over cooling components, which causes corrosion of contacts and components that lead to problematic and unreliable operation and premature equipment failure.
ABOVE RIGHT: Photos show the custom-manufactured control desks which are used for the manual bridge operation while the Semi and Automatic operation are controlled by the HMI (Human to Machine Interface) touch screen. One desk is for the traffic controls and the other for the bridge control functions.
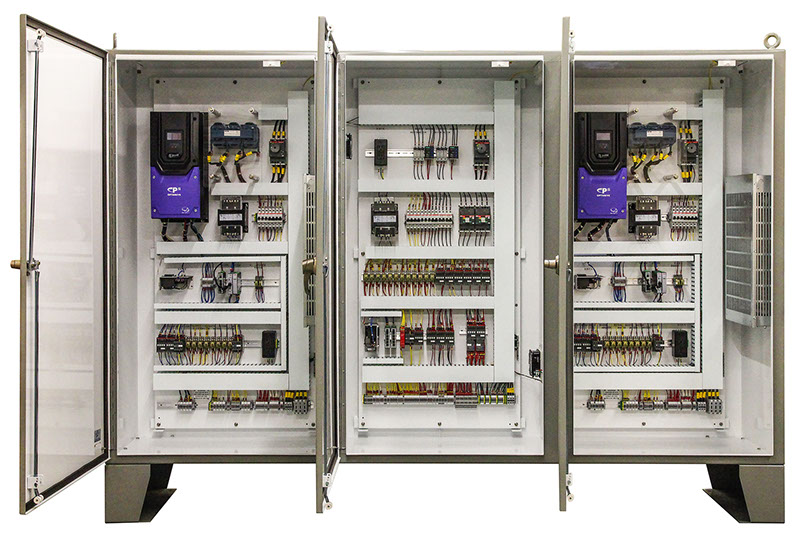
BELOW: Another set of custom-designed and built control enclosures which bolt together to form an L shape allowing them to fit across the corner of the control room where they act as a wire way to the control desks. They house all of the Ethernet TCP/IP communications along with the PLC and the HMI touch screen power supply. The Ethernet communications allow maintenance staff to view the status of all the equipment from a single location.
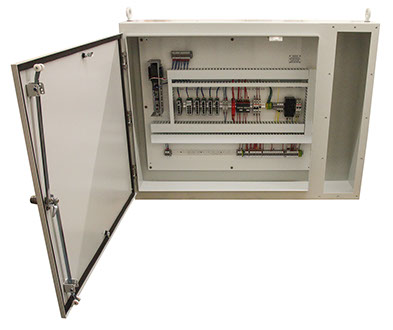
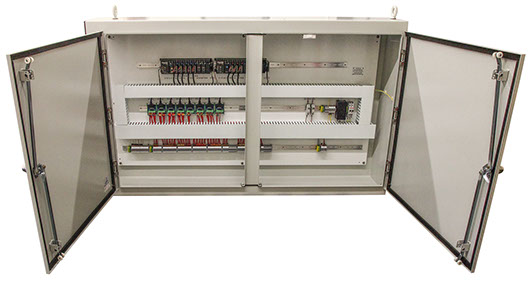
PROJECT CHALLENGES
The most common and widely used bridge control operation in use today would be to have an identical dual automated system so that in the event of an equipment failure, control can be switched over to the backup controls. This allows for bridge operation to continue while repairs are being conducted to the faulty equipment. Some bridges are also equipped with gas driven engines which allow for bridge operation to be conducted when there is no electrical power available or if a total control equipment failure takes place. The NASA bascule bridge control design called for three separate control modes to be used: 1) Full Automatic control. 2) Semi-Automatic Control, and 3) Manual Control.
The Manual Control, which uses relay logic to by-pass the automated PLC controls, has extensive wiring and has the necessity for a lot of cross interlocking between functions as can be seen in the photo below.
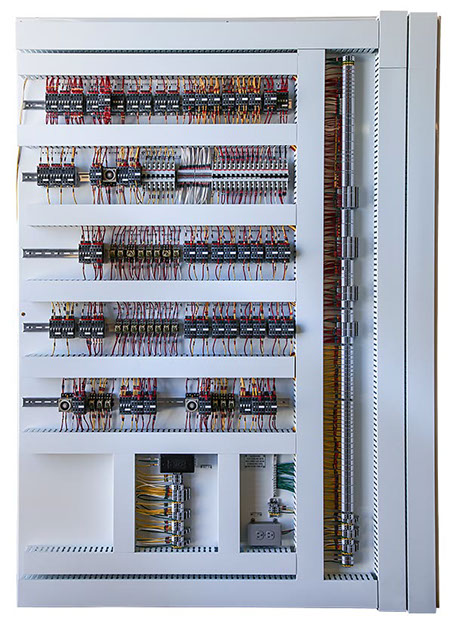
Design and construction of controls for NASA’s bascule bridge
When you are the world’s leading rocket testing company, the facility equipment had better be working properly and dependably. SID-TEC chose to use the Invertec ODP2 line of VFD’s (Variable Frequency Drives) for this project because of the P2’s advanced control features, which is what makes these drives an industry leader in the field of precision AC motor and machine controls. Using the powerful WEB SAVVY control software allows us to change and control both the speed and motor output torque seamlessly during the bridge operation.
The custom designed and built Marathon 2000:1 speed over torque motors with encoder speed feedback, enables the P2 Drive to be run in the Speed controlled Closed Loop Flux Vector mode, which provides a high degree of speed accuracy but still allows the motor torque output to be changed as needed. The ODP2 VFD comes with an active front end which all but eliminates the need for front end filters to keep the power factor at an acceptable level. The drive comes standard with a 0.96 power factor. One of the other important benefits of the P2 Drive is that during the Auto Tune function the drive finds the smallest pulse that the connected motor can convert into rotational rotor energy and then blocks out all smaller pulses. In doing so it eliminates the shaft energy which is the cause of motor bearing failure.
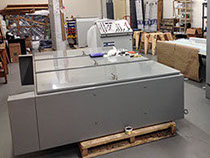
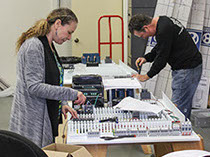
The panels were built by our staff at our air conditioned workshop facility in Largo Florida.
Shipping 4.5 tons of control cabinets to NASA’s Stennis site in Mississippi
The 4.5 tons of electrical control equipment was crated and shipped to the NASA site on a 52 foot air ride flatbed tractor trailer. Special care was taken to ensure all electronic components would arrive safely and in working order on the site. Custom wooden crates were assembled and built around the enclosures in Florida for a damage-free ride to Mississippi.
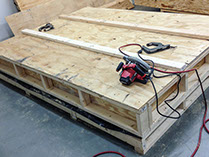
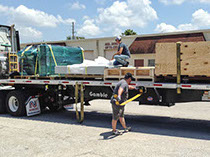

Custom Programming
SID-TEC’s engineering department wrote all of the PLC and HMI code (Human to Machine Interface) which has an interactive control and assimilated graphic displays that runs in real time to show the operator the condition of all parts of the bridge function at a glance. The HMI also has a full range of fault displays with a history archive database showing date, time and the description of the fault detected. These fault logs allows the maintenance people to detect and assess any areas that may require correction or repair.
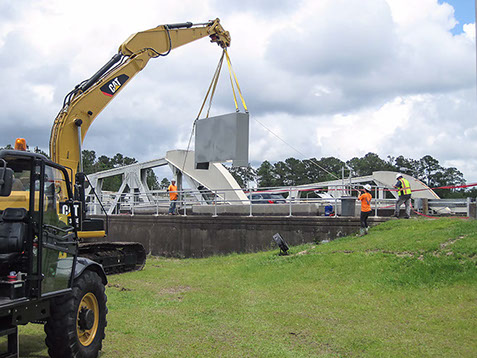
ABOVE: A CAT Loader lowers the three section span enclosures into the bridge work space below the road surface. Because each of the enclosures had a weight of around 5000lbs. NASA requested a larger loading capacity unit be used to safely install these enclosures.