SID-TEC increases production speed and
eliminates bouncing with an AC drive retrofit
on Duke’s Svedala Slewing Stacker Reclaimer…
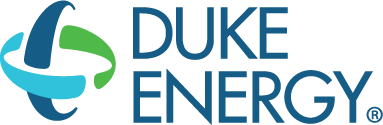

ABOVE: Duke Energy’s Svedala Slewing Stacker Reclaimer at a major Florida power plant. SID-TEC provided a motor and drive control upgrade that increased tonnage of coal reclaimed by over 50%. The single motor controller unit was replaced by individual controllers connected to each motor, ensuring each motor was operating at peak efficiency for its particular duty. This also eliminated system-wide shutdowns when problems with individual motors occurred.
PROJECT CHALLENGES
1) Resolving conveyor belt restart problems.
2) Fixing travel motor setup and overcurrent problems during maintenance.
3) Unwanted slew arm oscillations slowing production speed.
4) Bucket wheel bouncing problems requiring operators to run the wheel slowly.
SID-TEC was contracted by Duke Energy to upgrade the Motor AC Drives and conveyor belt Soft Starters on their Svedala Slewing Stacker Reclaimer.
Multiple problems to be addressed:
1) Each of the two conveyor belts had problems when they were being re-started if they were stopped with a load of coal still on the belt. SID-TEC resolved this by replacing the existing Soft Starters with the MS6 Pro line of Micro-Processor based soft starters which provide a current controlled torque ramp. This allows for the lowest current starting of an AC Induction Motor while at the same time allowing the motor to develop enough torque to get the motor and its connected load started and brought up to speed. These new Soft Starters now start the belt fully loaded or unloaded in a smooth trouble free manner.
ABOVE: Conveyor motor with new current controlling soft-starter which ensures efficient startup of the belt, both loaded and unloaded.
2) The 5 Travel motors were all connected to a single 125HP AC Drive that was being run in Volts per Hertz mode. This was causing problems with the load sharing of the motors. The motors, couplings and gearboxes were being damaged, and when this single drive tripped out the machine became inoperative. When a motor was removed for repair the remaining 4 motors were then subjected to much higher currents because the drive was set to run 5 motors. SID-TEC installed a new Back Panel with 5 individual Open Loop Vector AC Drives. Each Drive is set up to the motor and Auto-Tunes to provide each motor with the best performance control possible.
ABOVE: Breaking out individual terminal blocks allows for testing on each circuit and ease of connection and future maintenance.
A major problem soon became very evident, some of the Travel Motors wheels have a double flange and where being pushed up against the side flanges where the diameter is much larger and in so doing were propelling the machine faster than was expected and the motors who’s wheels were still running in the center normal position where being made to travel faster that they were set to travel and so the Dynamic breaking was being turned on full on these motor which were trying to slow down the machine. Fortunately by using one of the best brands of AC Drive SID-TEC was able to set the drives to accept and tolerate a speed difference of +/- 5% and in addition the Travel Drives were set up in a Master/ Slave configuration with changeover in the unlikely event that the Master Drive had a problem. This resolved the travel drive issues and no further Drive, Motor and gearbox issues have been experienced.
ABOVE: Each travel motor is now connected to an individual drive for maximum overall efficiency and power sharing.
3) The 2 Slew motors were connected to a single 30HP AC Drive. During the upgrade this was changed to having them connected to their own Open Loop Vector AC Drive. Once again the problems that had been masked by the single drive became very apparent when each motor was set up to its own drive. The Slew drive motors are in line with the machine on either side of the slew arm. When the machine is slewing (moving side to side) an oscillation is started by the mass of the bucket wheel and the equipment out on the end of the long arm. There is a push-pull effect on the motors, gearboxes and drive gears during the slewing motion. This effect was noticed by the SID-TEC Engineers when the slew was being moved in one direction in open air that there was a lot of twisting and skewing of the slew arm and that this was reduced when the arm was being slewed in the opposite direction, but this would change over when the arm was moved to the other side of the machine. In a discussion with the customer it was decided to put in a set of larger AC Open Loop Vector Drives and to set them up to each of the motor and auto-tune them, but set the overload and tripping in a separate Universal Process Controller.
4) The bucket wheel had been fitted with a new 200HP Open Loop Vector drive and this was Auto-Tuned to the motor and was working well, but there were occasions where the drive would trip out on an overcurrent.
ABOVE: Vector control drive ensures bucket wheel maintains consistent speed to provide maximized reclaiming tonnage.
The SID-TEC engineers viewed the machine under reclaim conditions and it was noticed that the slew speed was high and the bucket wheel speed was low. The reason was that the bounce being created at the end of the Slew arm was excessive and the operators were not able to run the machine in this manner. I was noticed that the Slew was pushing or trying to push the coal pile rather than to dig up the pile and reclaim it.
In a discussion with the customers the SID-TEC engineers decided to do some testing of the machine during recovery and see if the problem could not be resolved. The machine in its current setup was only capable of reclaiming 800 to 1000 tons per hour, which was way below the design and requirement needs of the customer. The bucket wheel speed was increased and the slew speed drastically reduced and this was tried, the effects were astounding there was no bouncing just a slight even movement as the digging was taking place. It was noticed that the slew would overshoot when stopping which was caused by an inefficient amount of Dynamic Braking and the speed of the bucket wheel pulling on the slew arm while digging. Larger Dynamic braking resistors were installed and the slew drive braking was greatly increased, with all the correct equipment installed the Reclaiming machine function was optimized.
SID-TEC’s retrofit changes increase production to 2,200 tons per hour!
The bucket wheel speed was increased to a point where bounce was being experienced and then the speed was set at a stable high speed value and then the slew speed was gradually increased and it was discovered that a 2 to 1 speed ratio was the best for the machine and the result was that the machine was now capable of reclaiming 2,200 tons per hour. This is the first time this has been achieved since the machine was installed 10 years ago.
ABOVE: A series of 3 Universal Processor Controllers connected via Ethernet to 8 motor controllers provide a sound and stable unified control of the machine.
CLIENT TESTIMONIAL:
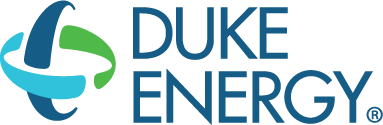