SID-TEC solves and improves DC motor speed control problems on a hundred-year old dual turret boring mill that was used to build WW2 tank turrets…
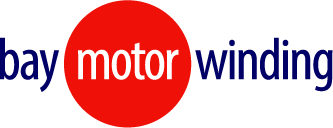
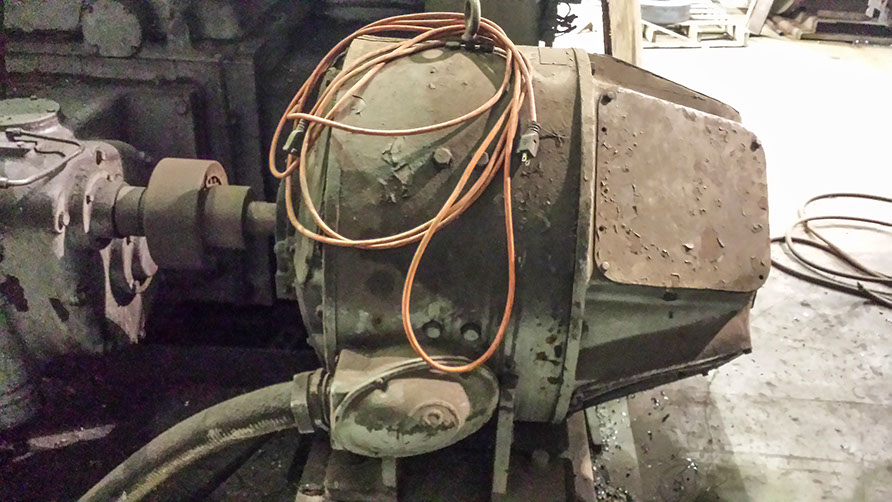
ABOVE: Ancient monster electric motor built in 1902 to run a massive rotary boring machine. It was used to machine turrets for tanks in World War II. SID-TEC was able to build a new motor control cabinet to give it decades of additional productive life.
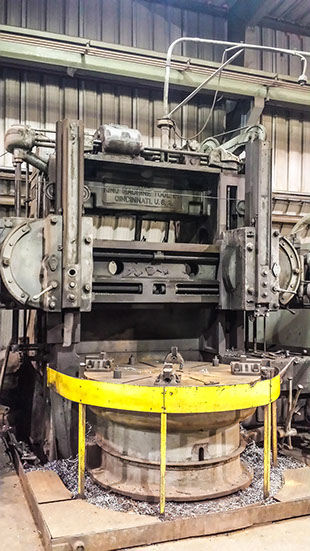
This shot shows the front end of the boring machine’s massive 62-inch rotating table. Materials are rotated past machining and cutting tools.
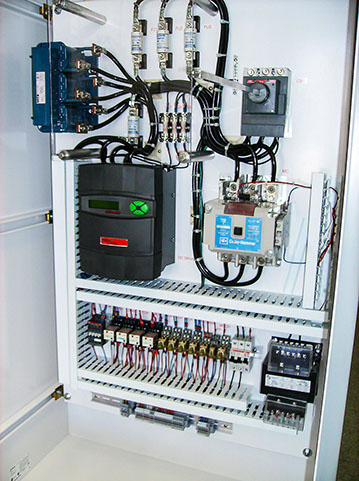
Here is the “after” solution created by SID-TEC to control the boring machine. The new electronics eliminated arcing and other operational problems, and provide additional life to this century-old machine.
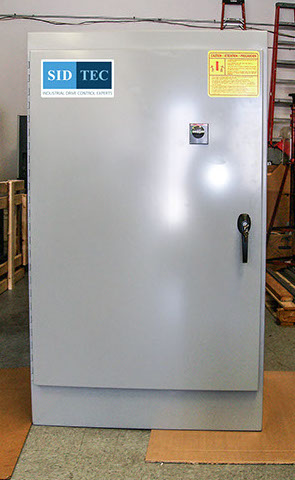
All the components in the photo at left are housed in the professional metal cabinet shown above. The cabinet was assembled off site and shipped to the customer for installation.
PROJECT CHALLENGES
1. Determining the advantages and disadvantages of keeping the original DC motor or buying a new AC motor.
2. Building a custom DC controller with all the modern benefits of current-day technology to coax several more highly useful decades out of this aging monster.
Durable old machine, built to last
This large DC motor is original to this 100 year old dual turret boring machine made by the King Machine Tool Company in Cincinnati Ohio USA at the turn of the last century. The machine has quite a history and was used to machine the tank turrets that were made and used in the Second World War.
The machine was built to last and the ridged structure and mechanical drive system of the 62 inch diameter rotating table are still true and work perfectly, even though the new owners, Specialty Machine of Gulf Port Mississippi, do not make the aggressive cuts this machine was once designed for.
The motor made by Crocker and Heller is only 30 Horse Power and boasts a maximum base speed of only 500 RMP and a top speed of 1500 RPM. The motor was originally built as a Compound Wound DC Motor and was controlled by a Ward Lenard Motor Generator set. Most of the companies that looked at rebuilding the control system wanted to get rid of this motor and replace it with an AC motor and VFD.
Still delivers amazing power
When SID-TEC was approached, the head of engineering did the math and figured out the output torque curve of the motor, he found that it was delivering 315 ft/lbs. of torque from 0 to 500 RPM. In addition the motor is capable of taking 200% for 30 seconds and 125% for extended periods of time, so this motor could produce an astounding 630 ft/lbs. of torque for short periods, and 400 ft/lbs. for extended periods.
A new AC drive would have been too expensive
Replacing this motor would require a 150HP AC motor and VFD to get the same job done, in addition the motor would have to be a 1000 to 1 torque over speed range vector duty motor and would require a lot of programming to handle to no load to full load changes as the cutting tool is applied to the job during machining. This AC option was becoming an expensive and unattractive option for the customer.
Modern controllers bring the beast back to life
SID-TEC’s engineering department decided to keep the old motor and do away with the motor generator set and fit a new state-of-the-art processor-controlled DC Drive onto the motor. A 3 phase Reactor was added into the armature circuit to soften the rate of rise of the current pulses produced by the DC Drive and the motor was overhauled. The compound winding was removed, allowing for a regenerative 4 quadrant controller to be used.
In addition a 1000PPR Encoder was mounted to the back of the motor shaft and this was used as a speed feedback device which provided the motor with a highly accurate speed regulation that provides the machine with a truly stable cutting ability and a very small no-load to full-load speed regulation.
CLIENT TESTIMONIAL:
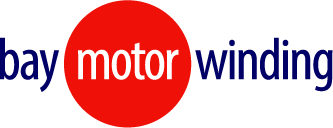
“As one of the owners and operators of Bay Motor Winding, I have seen quite a bit of change and innovation in the last thirty Years. The most significant innovation I have seen is the ability to control the speed of an AC motor with a VFD. This huge discovery has saved unimaginable amounts of energy when the applications are used on most fans, pumps and variable torque applications. There has been a big push to replace the old work horse of the variable speed motor industry, the DC Motor. At the same time these electronic starters [VFD’s, Soft-starters] are gaining a foothold. The “old timers”, the engineers that knew DC technology, have been retiring and leaving the workforce. The new engineers know very little about DC starters. The manufacturers and their sales reps are pushing the latest greatest AC drive and motor retrofit replacement. Never mind that the application that they are planning on re-engineering has worked beautifully for over 50 years — with very little down time.
“The application I am referring to was on a huge vertical mill in a local machine shop. Bay Motor had kept the machine running for the last ten years or so with no support from any manufacturer. The mill dated back to 1902 built by King Machine from Cincinnati Ohio. From what I was told it was used during its life time to machine tank turrets during WWII. The components consisted of a GE DC motor/generator to provide the DC voltage, an extremely worn out Word Lenard manual starter and a Crocker Heller DC Motor. The starter had been patched up and tinkered with for years and it was way past worn out.
“Every other component on this lathe was in remarkable shape. It just needed the controls to be upgraded. We heard from several manufacturers reps about the benefits of switching from “that old DC stuff” to new modern AC components. Newer and better technology was all they could rant and rave about.
“I kept going back to the fact it had worked beautifully for over a century, why throw the baby out with the bathwater? Once I decided we were going to stick with the DC Motor and replace the old motor generator and mechanical starter with a DC Drive, the search began. It took me over six months of asking everyone in the industry about this project. I was finally introduced to Mike and Joe with SID-TEC. After the initial visit to the job site by Joe we had a plan. We were able to propose the solution to the owner Ricky Bishop of Specialty Machine and were given the approval immediately.
“SID-TEC designed and built the controller at the facility in Clearwater and shipped it with all of the controls to Gulfport within weeks. The following week, Mike Holdsworth the head of engineering at SID-TEC showed up to oversee the install and commission the job. Upon installation and startup of the system, we discovered the old DC Motor had been limping along under half power. We pulled the motor, brought it back to our shop (only minutes away) and rebuilt it. This gave Mike a few days to hit the links. Once the rebuilt motor was in place, Mike was back on the jobsite tuning and programming and training the machinist on the operation of the system.
“SID-TEC proved to me that they can make an old DC machine operate better than it did when it was new. The speed control of this motor is so smooth. The quality of the products produced are better than before. When working with SID-TEC on this project, I knew we would have a positive outcome. With SID-TEC as part of my team, I now search out DC control projects.”
— Patrick Benvenutti, Bay Motor Winding,
Gulfport, Mississippi