DC drive retrofit brings overheating problems under control for plastic extrusion machinery…
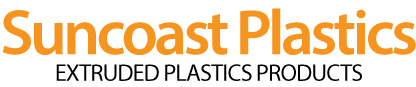
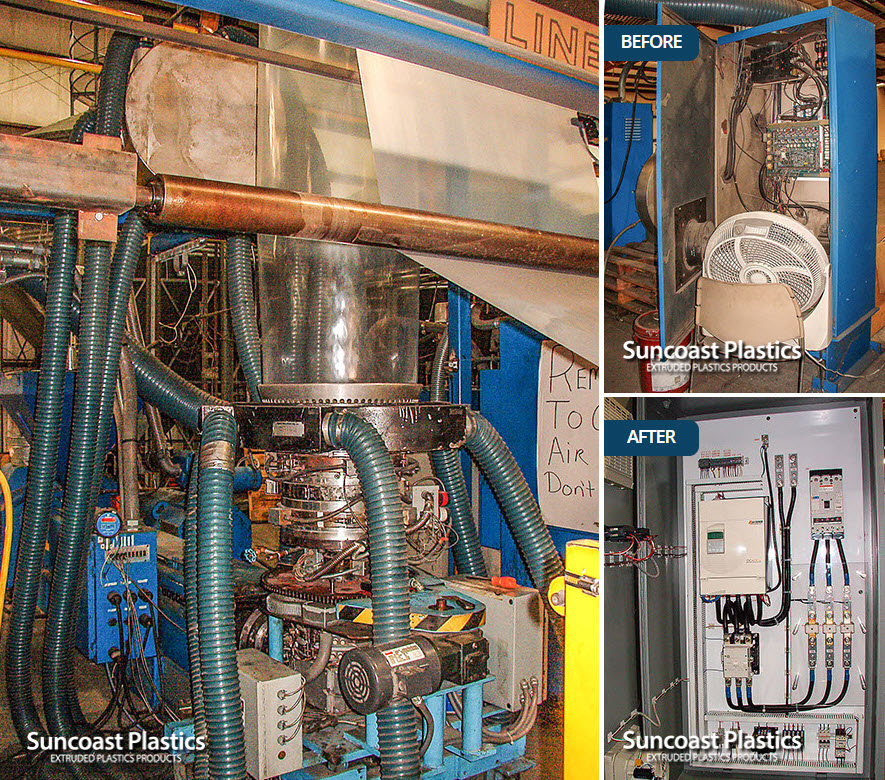
ABOVE: Photo of the blown film extruder line showing the die with the air delivery tubes and a plastic tube being extruded and drawn out of the machine. Dust and heat problems were causing frequent repairs and limiting production runs. SID-TEC’s retrofit upgrade and new cabinet removed ALL the problems so that the equipment simply worked the way it was supposed to.
The “before” shot shows the cabinet door open and a household fan blowing into the drive cabinet to attempt to prevent overheating. The “after” shot shows a retrofitted cabinet with optimized controls and a filtered cooling fan that ensures consistent operating temperatures.
PROJECT CHALLENGES
1. Heat buildup problems causing downtime and maintenance issues.
2. Extending the life of existing machinery with drive and motor retrofits.
The basic problems are plastic dust and heat
The workhorse of the plastics extruder world is the main motor which turns the screw. These drives and motor do not have to be very special but they do need to provide a reliable constant speed and must be able to produce a lot of horsepower for long periods of time.
This has made the shunt wound DC motor with its constant torque output and DC6 Drive the combination of choice for many years in the plastics extrusion industry.
When problems with these drives and motors are encountered, they all stem from excessive heat. The plastic dust which accumulates and attaches itself to the components forms a coating which increases the buildup of heat in the DC Drives. This dust and heat is forced into the motor by the cooling fan which chokes up the cooling veins and causes hot spots within the motor windings.
Loss of current pulses increases power draw and heat
Each DC Drive, regardless of brand name or manufacturer, which is connected to a 3 phase AC supply and has 6 SCR, gives off 6 current pulses for every complete cycle of the 3 phase AC. When an SCR fails or is no longer able to turn ON in any number of ways, two current pulses are eliminated from the usual 6 and the remaining 4 current pulses that are conducting current to the motor, will increase in current value in an attempt to make up for the loss in power being delivered to the motor. This current increased which is attempting to compensate for the loss of power to the motor only makes matters worse and even more heat is generated in both the Drive and Motor.
DC drive and motor replacement adds years of extended production
The physical extruder machine and motor may be in great shape and capable of years of additional service. It is very worthwhile to have a new DC Drive installed to allow for good continuous production. It is always best to update both the drive and the motor at the same time. We have seen instances where only the DC Drive has been replaced, and the results and reliability are not nearly as good as when a total replacement of the drive with all its additional components and wiring have been retrofitted.
New cabinet and cleaning of motor air channels ensures optimum operating temperatures
When SID-TEC does an extruder drive retrofit, care is taken to ensure adequate cooling for the drive has been built into the Drive Cabinet. In addition, the main motors cooling fan is completely cleaned, along with the motor air channels to ensure that proper cooling is once more in effect for the equipment.
The plastics extruder environment is a hot one with the heat being applied to the barrel and plastic exit path into the blown film die section or slot dye, so it is important to have a large air flow volume to ensure proper cooling.
As can be seen by the above before and after photos, the before has the cabinet door open and a house hold fan blowing into the unit in order to keep it running while it is overheating, also note the size of the panel cooling fan and filter kit in the after retrofit panel.
DC drives and motors generate considerably less heat than their AC counterparts
In today’s AC Drive world we see a lot of companies wanting to convert their DC Drives over to AC Drives and motors. While this can be done, please keep in mind that a in a DC Drive, 7% of the total power that passes through the Drive is converted into heat, and that in an AC Drive, that percentage increases to 25% heat conversion. Since heat is the main killer of drives and motors in the plastics extrusion industry, it is usually much better to use DC drives and motors. Our engineers are very experienced with both DC and AC drives and can recommend the correct components that will optimize your machinery to give you the longest life with the fewest problems